Preventing Weld Undercut Made Easy: Trick Techniques Revealed
Wiki Article
Mastering the Art of Welding: How to Avoid Undercut Welding Issues for Flawless Fabrication Results
Effectiveness and precision are vital in the globe of welding, where also the tiniest flaw can jeopardize the architectural integrity of a made piece. One typical obstacle that welders face is damaging, an issue that can weaken a weld joint and lead to expensive rework. By recognizing the origin of undercut welding and executing effective strategies to stop it, welders can raise their craft to new degrees of excellence (Preventing weld undercut). In the quest of flawless construction outcomes, understanding the art of welding to stay clear of undercut problems is not simply an ability however a requirement for those aiming for excellence in their work.Recognizing Undercut Welding

To protect against undercut welding, welders must guarantee correct welding specifications, such as readjusting the current, voltage, traveling speed, and maintaining the proper electrode angle. By understanding the reasons of undercut welding and applying precautionary actions, welders can attain top notch, structurally audio welds.
Root Causes Of Undercut in Welding
Comprehending the aspects that contribute to damage in welding is important for welders to produce premium, structurally sound welds. Inadequate welding inaccurate or current welding rate can also add to damage. Recognizing these reasons and applying proper welding techniques can aid avoid damaging concerns, guaranteeing sturdy and strong welds.Strategies to stop Undercutting

To alleviate the threat of damaging in welding, welders can utilize critical welding methods intended at improving the top quality and stability of the weld joints. In addition, using the right welding technique for the details joint setup, such as weave or stringer grains, can contribute to minimizing damaging.
Utilizing back-step welding techniques and regulating the weld grain profile can likewise help disperse warmth uniformly and decrease the risk of undercut. Normal assessment of the weld joint during and after welding, as well as implementing high quality assurance measures, can aid in identifying and dealing with damaging concerns without delay.
Significance of Proper Welding Specifications
Selecting and maintaining proper welding specifications is important for attaining effective welds with marginal issues. Welding specifications refer to variables such as voltage, existing, take a trip rate, electrode angle, and shielding gas circulation rate that straight influence the welding procedure. These specifications should be meticulously adjusted based upon the kind of material being welded, its density, and the welding strategy utilized.Correct welding specifications guarantee the correct amount of heat is used to melt the base steels and filler material evenly. If the specifications pop over to these guys are established too expensive, it can bring about too much warmth input, creating burn-through, spatter, read the full info here or distortion. On the various other hand, if the specifications are too low, insufficient fusion, lack of penetration, or undercutting might happen.
Quality Guarantee in Welding Workflow
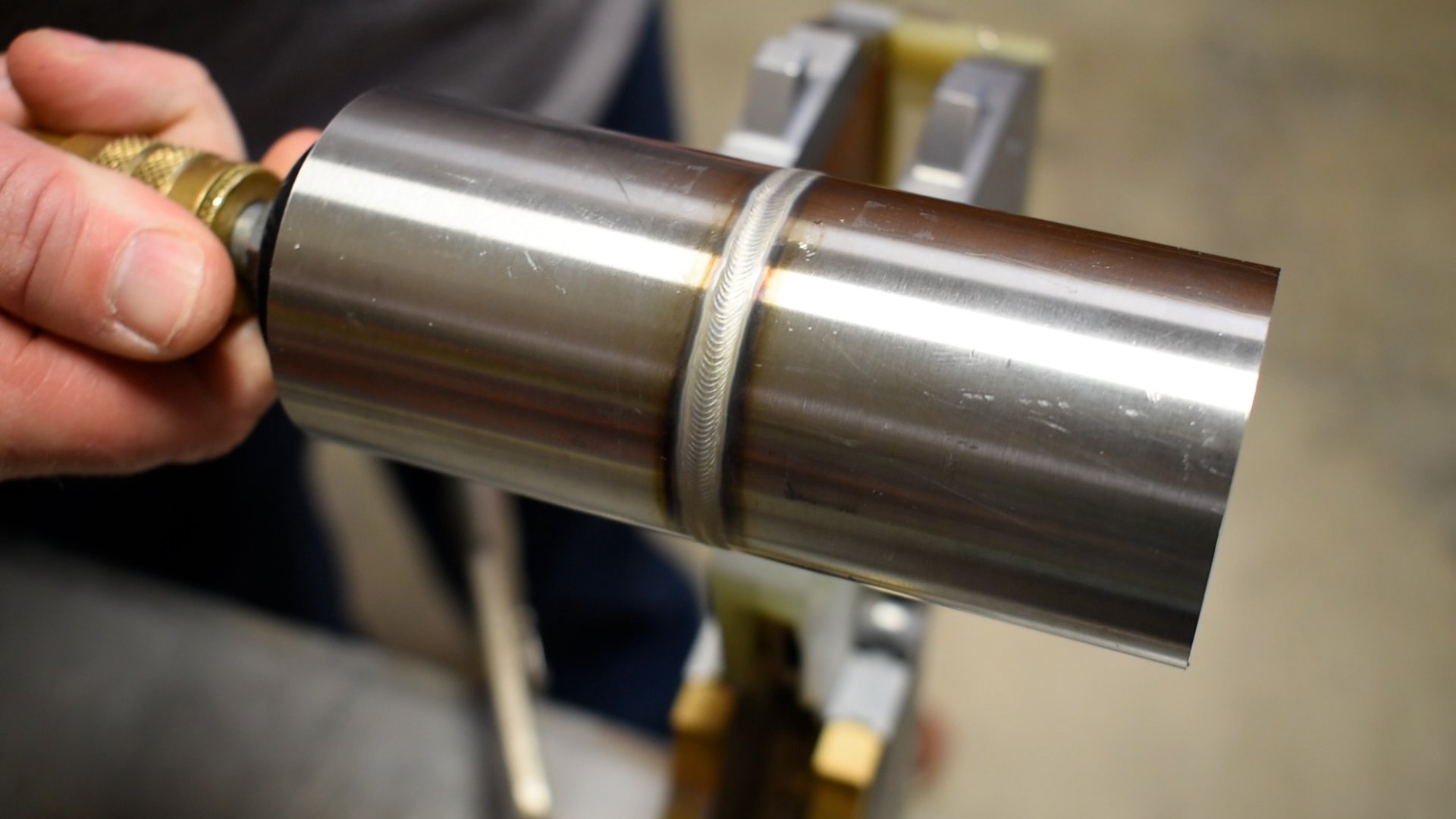
Conclusion
In verdict, understanding the art of welding needs a comprehensive understanding of undercut welding, its causes, and methods to stop it. By guaranteeing appropriate welding parameters and executing top quality guarantee practices, flawless construction results can be accomplished. It is important for welders to constantly aim for quality in their welding operations to avoid undercut problems and generate top notch welds.Undercut welding, a typical defect in welding procedures, happens when the weld metal doesn't correctly load the groove and leaves a groove or clinical depression along the bonded joint.To prevent undercut welding, welders ought to ensure correct welding specifications, such as adjusting the current, voltage, traveling rate, and keeping the right electrode angle. Inadequate welding present or inaccurate welding rate can additionally contribute to damage.To mitigate the risk of undercutting in welding, welders can utilize strategic welding strategies intended at enhancing the quality and stability of the weld joints.In conclusion, mastering the art of welding requires a complete understanding of undercut welding, its causes, and strategies to prevent it.
Report this wiki page